We usually use the air compressor for various purposes. Every time, we prefer more efficiency and faster performance from the machine. But How to Make Air Compressor Faster? What makes the compressed air system much more robust?
A faster air compressor quickens work, lessens downtime, and increases growth. Almost 70% of the workers need compressed air to operate their air equipment and finish the operation quickly and easily. After a while, the compressor started to grow slower and more void. Your air compressor potentially encounters the same difficulty.
Maintaining the integrity of your whole pneumatic system is vital to getting the most value from the air compressor. We hope that this post will energize your workforce. However, you might be asking what techniques could be useful for operating the compressor more effectively. Check out the entire article to find out the best ideas you can utilize in the workplace.
How to Make Air Compressor Faster – 10+ Awesome Tips
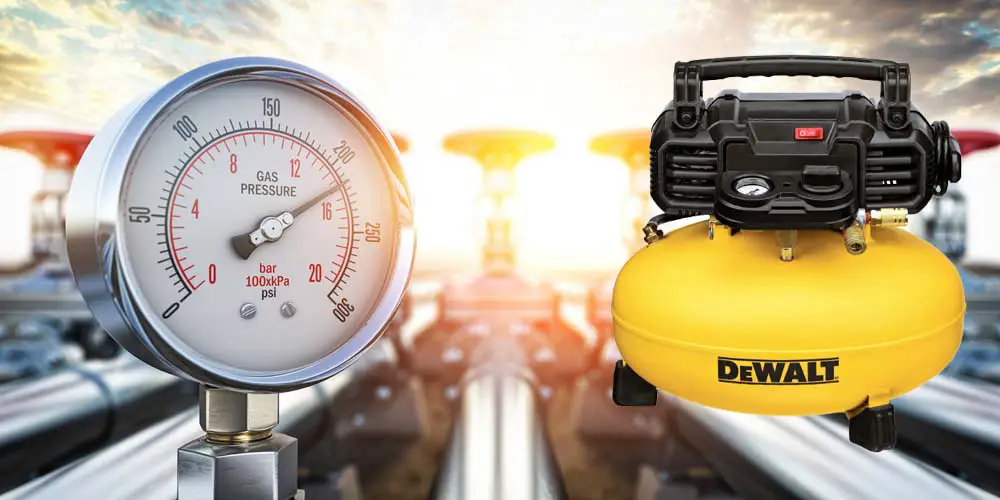
Tip 1 – Learn About Machines Pressure Gauge
First, become familiar with every component of the compressor. If you are familiar with how they work, you can keep it running faster and faster. For example, learn about electric tanks, pumps, motors, and receivers.
Look for a gauge on your air compressor that is connected to a nozzle that exits the air tank. This pressure gauge is for the air tank. Determine the outlet pressure gauge that is connected to the airline of the compressor. You can check the air tank pressure gauge by checking the backup air pressure. Also, find the outlet pressure gauge to see the outflow of air pressure.
Tip 2 – Use the Adequate PSI
Check the PSI specifications for the air compressor. Although large equipment associated with stationary systems usually requires more than 10 cubic feet per minute at 100-120 pounds per square inch (psi), also, the air tools meant for general use with portable air compressors necessitate 0-5 cfm at 70-90 psi.
Need to know how to get more CFM out of air compressor? See simple user guide here.
Tip 3 – Modify Pressure Regulator
Another crucial step is adjusting the pressure regulator. Connect the airline hose of your selected pneumatic tool to the air compressor. To minimize the pressure, turn the pressure regulator knob in the opposite direction. To enhance the pressure, turn the pressure regulator knob in a clockwise direction. The working time can be shortened with appropriate calibration.
Tip 4 – Utilize FRL Technology
To maintain air compressor systems at maximum process conditions, manufacturers use a technology known as an FRL (filter, regulator, or lubricator). The FRL system has an airline filter, a pressure regulator, and a lubricator as major components. It’s also great for effective performance.
Tip 5 – Change The Filter
Why do we install filters? Filters are settled in the air upstream of regulators, lubricators, control valves, and air-driven machines, including cylinders and air motors. Sometimes you need to change the side of the filter to allow it to run more quickly.
Filters can become clogged with dust, grime, and grease, which lowers system air pressure. It has an indirect channel that links to a foam filter. So, altering and installing filters may help you minimize your work time.
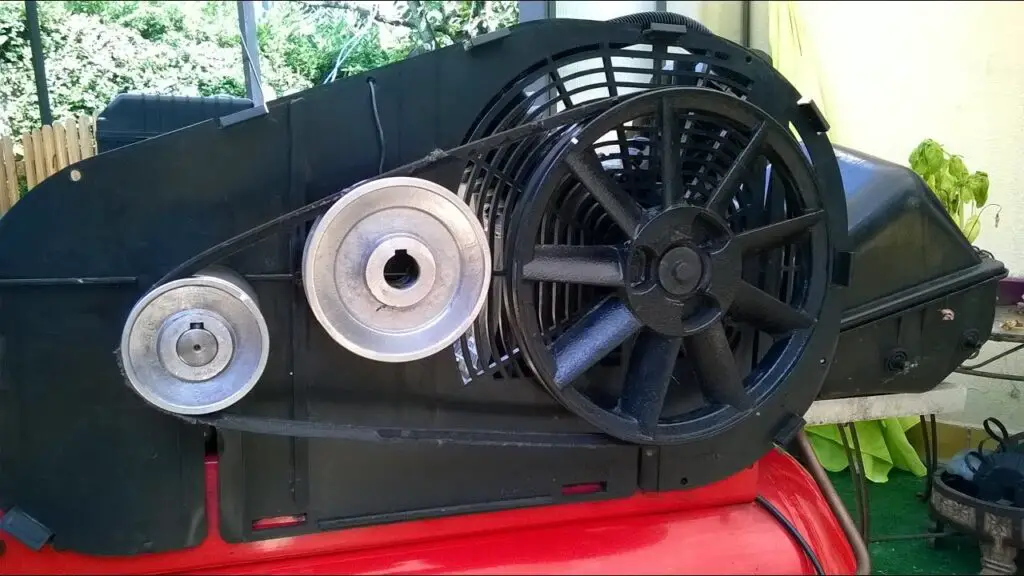
Tip 6 – Maintain Cool Intake Air
Keeping the intake air temperature low might be quite beneficial for you because a hot air compressor can seriously affect performance. Therefore, check to see if the intake air is not too hot.
The compressor utilizes less energy to compress the air when the intake air is cooler. Additionally, cooler intake air might improve productiveness by 40%. A 20-degree drop in temperature can reduce expenses by about 3.8%. By using the compressor motor, you can use less energy to compress air.
Tip 7 – Keep the Size of the Compressor Small
Large and bulky compressors are typically inefficient since it takes more time for them to fill the tanks needed to deliver pressurized air. Yet, installing multiple compressors is a good idea if you want faster performance.
Alternatively, you can use a small compressor to make it run more quickly. You do not require 5 CFM for a little work in your household. The majority of portable compressors feature motors that range from ¾ HP to 5 HP. Additionally, a system with less horsepower capacity will need less electricity to run the motor.
Tip 9 – Use A Short Air Hose
Long pipes between inlets or outlets have more flow resistance because of metal-on-metal friction. The compressor’s efficiency and CFM output will suffer with longer hoses. But, the resistance will be reduced if you use a short tube.
The use of short hoses is indeed required since pressure drops in the pipeline impact your compressor’s functionality. A 1/4″ hose diameter can result in more air interaction with the hose body. So, it’s better if you select a 3/8-inch air hose. But don’t forget to check the hose’s thickness or diameter.
If you are looking for ways to increase CFM on your air compressor, check related post here.
Tip 10 – Make Sure You Maintain High Pressure
Maintaining high pressure on your machine is vital. To get to an air tool, the air must move a considerable distance. The settings on the air compressor generate a changing or continual high pressure.
Air compressors can increase system stress and lower productivity as they operate closer to full pressure. Therefore, you should maintain a high air pressure to prevent a drop in pressure. Limit the airflow as much as possible.
To accommodate user peaks, leaks, pressure drops, and supply variations, numerous air systems operate at high pressures. Operating at high pressures can, however, demand up to 25% extra compressor horsepower. Alternatively, you can use a flow controller.
Tip 11 – Upkeep of the Piston Cylinder
Remember to check the piston cylinder arrangement. You might need to detach the connecting rod and crankshaft. Usually, dirt is what causes problems, so be certain to stick to the advice we’ve provided below.
- Use pressurized air to wipe away the particles that block your piston cylinder.
- Put a clean towel over the cylinder and piston after removing them from the crankcase to collect any dirt.
- Reduce too many chemicals by using a cleaning solution.
- You can lubricate them every day to keep them running faster.
Tip 12 – Restrain Pressure Drop
The generated compressed air moves from the tank to the air tools. Sharp turns and long pathways create a lot of friction and lower pressure at that point, which ultimately slows down the work. Therefore, fewer delivery lines are required and you need to think about pressure drop, which may happen due to inadequate pipe size, moisture development, filthy filters, or extended air travel distances.
There will be some pressure loss in the pipeline since air compressors require an air motor to operate the diaphragm. So, you need to properly maintain and check the compressor machine. The best course of action is to maintain or swap out damaged parts.
Tip 13 – Clean The Air
Cleaning the air is another action to speed up the machine’s functioning. In essence, air-holding dirt slows down the machine. Therefore, passing clean air is important for faster compressor performance. And for clear air, be sure to change the filter.
Want to know how to build a high pressure air compressor? See step-by-step guide here.
How to Make Air Compressor More Powerful: 6 Effective Solutions
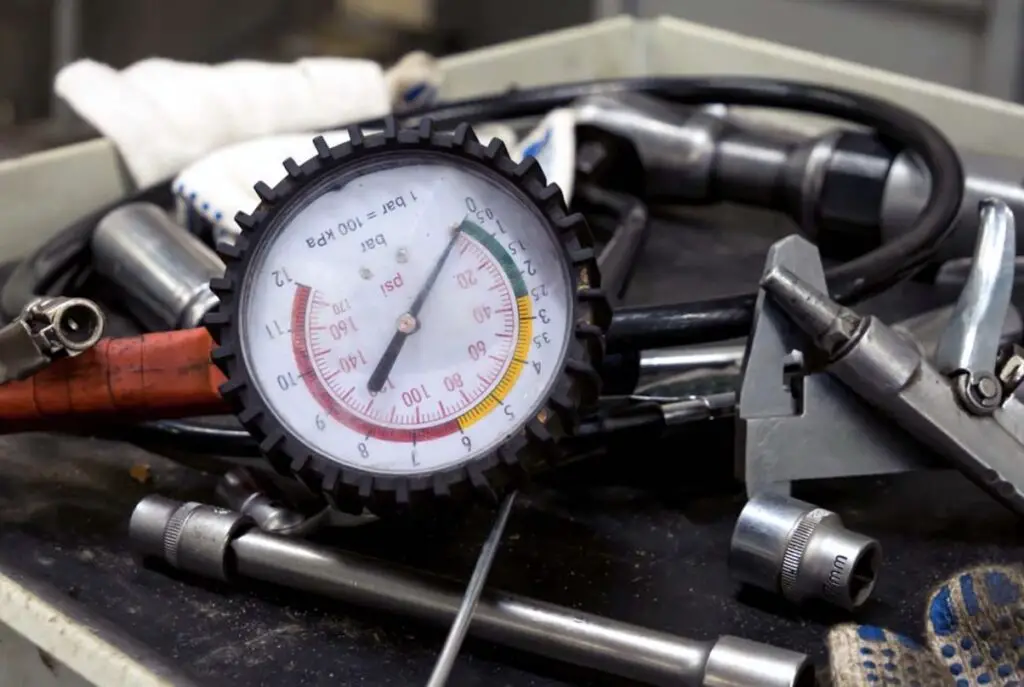
1. Use Speed Drive
If you expect effective performance, go ahead and add the variable speed drive compressor. Generally, the motor receives certain amps and voltage from variable speed drives.
The variable speed drive changes the speed of the motor to accommodate the air demand in order to preserve the system pressure. It happens after the compressor monitors the pressure in the air system. You should also know that it can reduce an industrial plant’s energy consumption by up to 35%.
2. Check For Energy Recovery
Energy recovery is another part of making the machine or any electrical tool perform efficiently. However, you must remove them from the air and cool this warm air before using them.
3. Fix The Leakage
Oil leaks are a fairly regular factor that could influence compressors. It might ruin your compressor and have an effect on its performance. Air leaks are a silent killer We usually notice leakages on fittings like hose couplings, pressure regulators, joints, and disconnects.
Leaks cause the average system to lose approximately 25-35 percent of its energy. A 100 psi system with an eighth-inch diameter leak can cost more than $12,000 worth of energy every year. So, it’s quite crucial!
Use a cost-effective ultrasonic leak detector to develop a leak-free system. On the threaded connections, Teflon tape or pipe joint compound can help enormously. Additionally, we suggest cleaning the hose and its connectors by using a soapy water solution. You will notice a bubble in the leak.
4. Get Auxiliary Tanks
We generally prioritize satisfactory accuracy, which we can achieve with the use of auxiliary tanks. It helps by reducing the frictional loss between the hose and the air, and it helps in extending the length of the hoses.
5. Regular Lubrication is Good
When the compressor is properly lubricated, mechanical tools operate more effectively and efficiently. It helps to decrease wear and friction. However, synthetic oil and lubricants can be a lifesaver.
Compressor oil is an essential part of keeping a healthy compressed air installation. Oil serves primarily as a cooler as it removes the heat during compression. Additionally, it picks up all the particles and transports them to the oil filter to resolve any issues. So, run the machine like a horse by lubricating it properly.
6. Maintenance And Repairs
The compressor can perform more rapidly and effectively with regular maintenance and repairs to the damaged parts. The compressor could have internal or exterior troubles. So, make sure you assemble the hoses, modify the filter, clear the dirt, tighten nuts and bolts, clean the intake valves, and check to see if anything needs to be fixed.
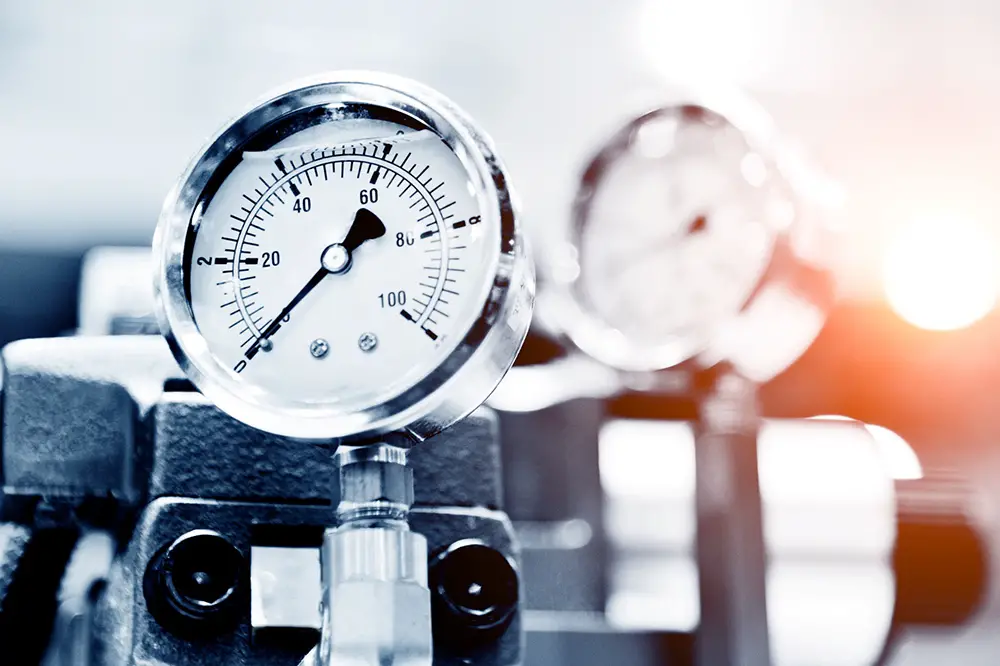
Looking for the best air compressor for spray painting? See detailed review here.
FAQs
How can we fill a compressor tank faster with air?
1. To check the compressor efficiency, do the FAD test.
2. Use a small-sized compressor or multiple compressors to fill the tanks.
3. Make sure to check for unaddressed leaks since they will prolong loading time and tank filling time.
5. Modification of the pipeline for compressed air is important.
6. Use GI or MS pipes rather than aluminum plumbing. Due to the tendency of GI or MS to deteriorate over time, Al has a lower coefficient of friction.
How fast should an air compressor run?
It usually takes 0 to 5 cubic feet per minute at 70-90 pounds per square inch to operate commonly used air tools with portable air compressors. Additionally, an industry norm for a motor is 800-900 rpm when it is linked to the maximum horsepower of the pump.
How does a high-pressure air compressor work?
By applying pressure to ambient air, air compressors generate potential energy that is stored in a tank. The pump unit produces an air pressure of 175 psi and has two pistons, one large and one mini. The main cylinder’s output passes into the smaller cylinder’s input, where the air is compressed at high pressure.
How long can a compressor run continuously?
Generally, vane and rotary screw compressors are made specifically for an all-time or 100% duty cycle. But standard air compressors can be left working for about a few hours to up to 24 hours a day, based on their size and type.
Final Thoughts
Now we hope you know How to Make Air Compressor Faster and make them more efficient. We have shared all the common reasons that slow down your equipment as well as all the best ideas that will enhance the performance of your compressor.
With the proper care and maintenance, you can run it the way you expect! However, if you find any other trouble regarding the air compressor or pneumatic system issues, leave your query. We would love to share the best solutions.
Right here is the right webpage for anyone who really wants to find out about this topic.
You understand a whole lot its almost tough to argue
with you (not that I personally will need to…HaHa).
You definitely put a fresh spin on a subject that’s been written about for
many years. Great stuff, just great!
Hi there! Thank you! Glad you find it useful)